Würth Industrial US - Customer Case Study
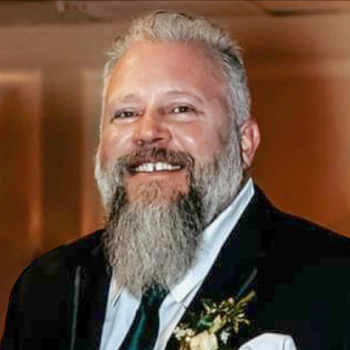
Business Solutions Manager
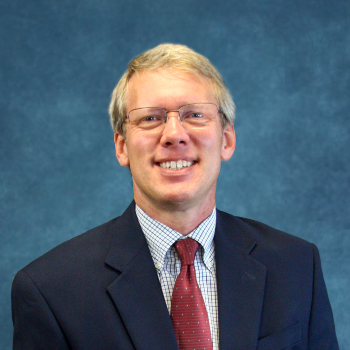
Integrated Solutions Engineer
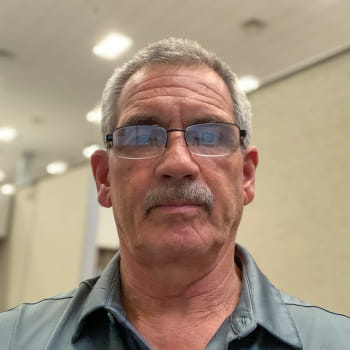
Systems Engineer
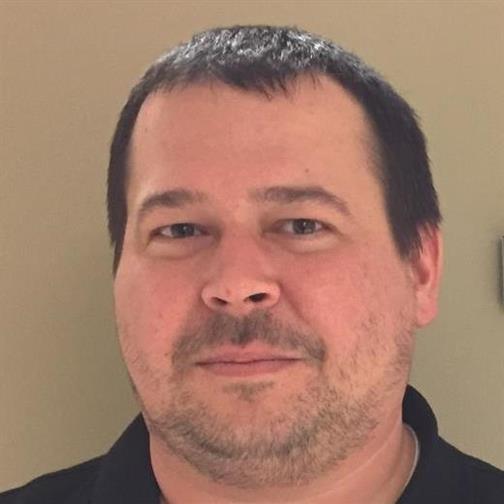
Project Engineer 2
Würth Industrial US, located in Brooklyn Park, Minnesota, identified an opportunity to improve the efficiency of its AS/RS system. The focus of the efficiency improvements was on inbound processing and material handling. The manual and time-consuming process of breaking down pallets, repackaging heavy hardware into totes, and carrying them to the AS/RS induction conveyor was slow, costly, and posed ergonomic challenges.
A collaborative effort between the Würth Industry team, Casey Wand (Project Engineer 2), Scott Carrico (Business Solutions Manager), and Dave Leversen (Integrated Solutions Engineer), along with the expertise of our supplier, Industrial Kinetics, addressed this challenge. The result was the development of an innovative system featuring pallet conveyors loaded by a lift truck and indexed to the operator station one at a time. At the operator station, a lift and rotate table with a powered conveyor on top enabled the operator to manage the loading task efficiently from a single position at an ergonomic height.
Original Concept:
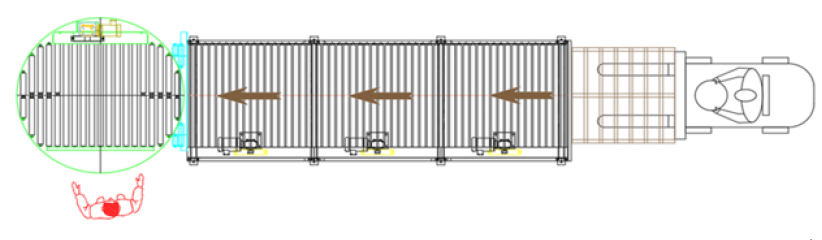
The system incorporated additional features, such as a fork truck sensor to prevent the pallet conveyor from moving while loading and heavy-duty fork truck guards at the ends.
Don Hughes, Systems Engineer, played a crucial role in the project, ensuring Würth Industry's requirement for substantial installation before the end of 2023 was attainable. Working closely with Industrial Kinetics, Wand and Hughes finalized the design, which Würth Industry quickly approved.
During the process, Würth identified a need to move to the next pallet before completely depleting the current one. The original design allowed the operator to slide each empty pallet off the lift/turn table and stack them for later pick up. However, with the product still on some of the pallets, a lift truck needed access to the operator's end of the system to remove the pallets. An angled section of gravity conveyor and additional controls were seamlessly integrated into the system to address this. This modification allowed the operator to power the pallets off to a single-position outfeed gravity lane, where a lift truck could efficiently pick them up.
Final Design:
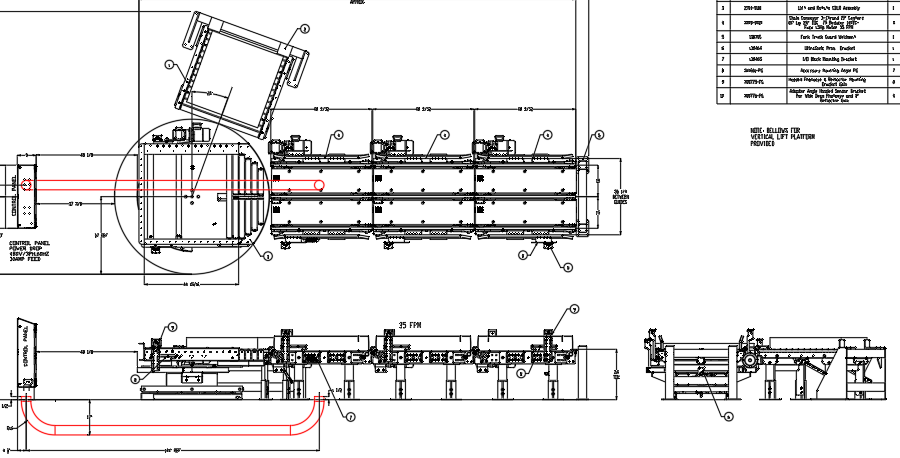
Working together to solve this roadblock, Associated successfully met the timeline. The Factory Acceptance Testing (FAT) took place on December 20, 2023, and Wand and Hughes completed the installation on December 28, 2023, just before the end of the year.
This collaborative effort resolved operational challenges for Würth Industrial US and showcased the agility and efficiency of the Associated team in delivering a tailored solution to enhance productivity and ergonomics.
-
FAT
-
Installation: Operator Station
-
Installation: Load End and Drag Chain Conveyors
Real World Solutions. Change The Way You Do Business.
For more information about Solutions we offer, please fill out the form below.